Architecture as a field of study and innovation has constantly been in a state of change. Over the years, the methods of practising architecture, the presentation drawings, the conceptualization processes have been using various methods to ensure the end product to be relevant to the current era. The introduction of the word ‘Digital’ in architecture has changed the entire approach towards this subject. Digital architecture has introduced various software, tools, and portals that have eased out our lives and have initiated innovations on a large scale. Digital Fabrication is one such progressive step that has allowed architects and designers to bring revolutionary changes in their architectural practices.
The fabrication process has allowed us to ease out design processes that were before almost impossible to execute. The digital fabrication laboratories are also known as digital labs have been emerging all around the world to create these designs. The digital fabrication is an exact method with the precision that even allows less wastage of the products, less time consumption, and more efficiency.
The digital fabrication is divided into three types:
- Additive manufacturing
It emerged in 1983 where an ultraviolet laser beam was projected into a mass of photopolymer which later turned into solid plastic. First, it was only centric to plastic as an end material but now, metals, clay, glass are being used to do this procedure. Many further innovations are allowing more and more materials to be a part of this manufacturing process.
- Subtractive manufacturing
In this method, an object is carved out of an existing block. This method has been extensively used, its precision is what makes this one of the highly used methods in the fields of digital fabrication. Laser-cut models, conventional model-making techniques all fall under this category of manufacturing.
- Robotic manufacturing
This method is one of the most progressive ones in the fields of fabrication. It allows manufacturing products with bends, folds, etc. The advancing of these robots depends on their configurations.
Architecture and Digital Fabrication
The Indian artist Ruchika Grover heads a product design studio that explores the fabrication process of natural stones. These stone surfaces are created through a unique process of digital manufacturing with hand craftsmanship.

The process starts by conceptualizing an end product through sketches and studio discussions in a two-dimensional drawing which is later, extruded according to the heights and depths. A range of patterns, material, and tools for the same is employed. The material after cutting is later finished by traditional artisans that work through the process of chipping, sanding, and shot blasting.
Neri Oxman also is known as a Bio-architect has been at the forefront of exploring digital fabrication with the use of natural materials. She has developed water-based biocomposites for fabrication. The project is named as Aguahoja and has an exhibit of a pavilion and a series of artifacts. It focuses on the importance of having water in the natural system. It explores the ideology of nature which has the innate quality to produce, decay, adapts, and reuse its materials again and again. This is done through the addictive manufacturing process of digital fabrication.
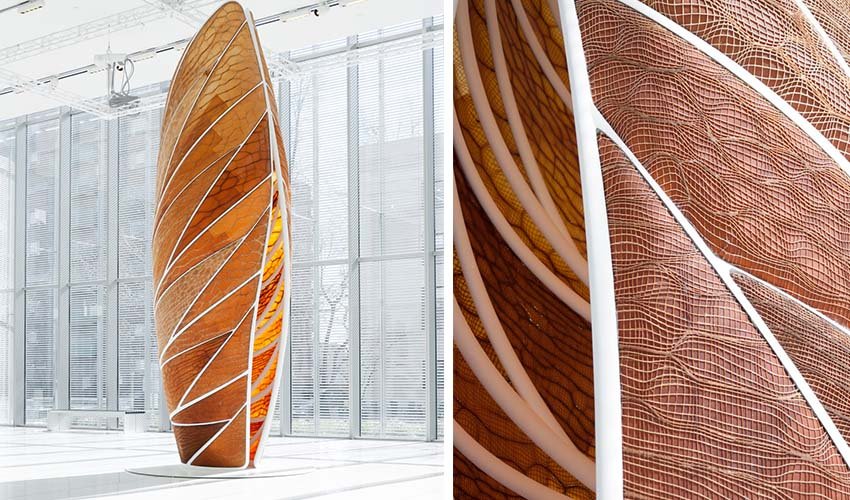
Another example would be the Chinese Pavilion at the 2018 Venice Architecture Biennale. This was themed as ‘Building a Future Countryside’ which had a core aim to explore new technology. This digitally fabricated pavilion has a twisting form which creates openings in a sequence of open and semi-enclosed areas. The robotic printing technology has been used to achieve this form and was developed by Philip Yuan.


The plastic used in this is recyclable in nature that helps in portraying an environmental issue of the Chinese countryside. The waved geometry allows many interesting forms a space within the pavilion, it creates nooks and corners for people to unwind and sit. This pavilion used fabrication technology to showcase its technologically progressive thought and yet sends a sustainable message by the choice of its material.